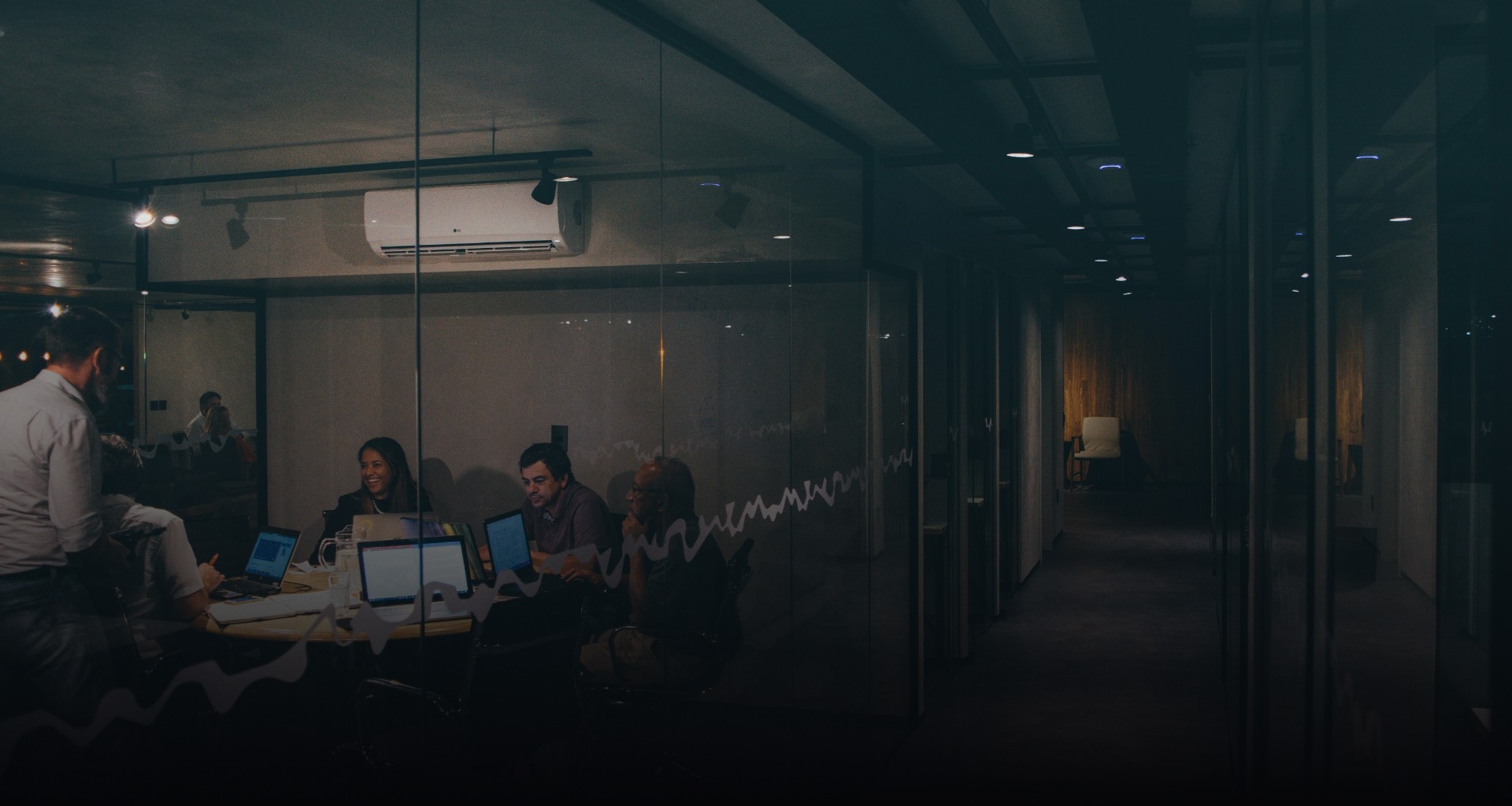
CASE STUDY: From Data Fragmentation to Delivery Excellence: A Case Study in Operational Improvement
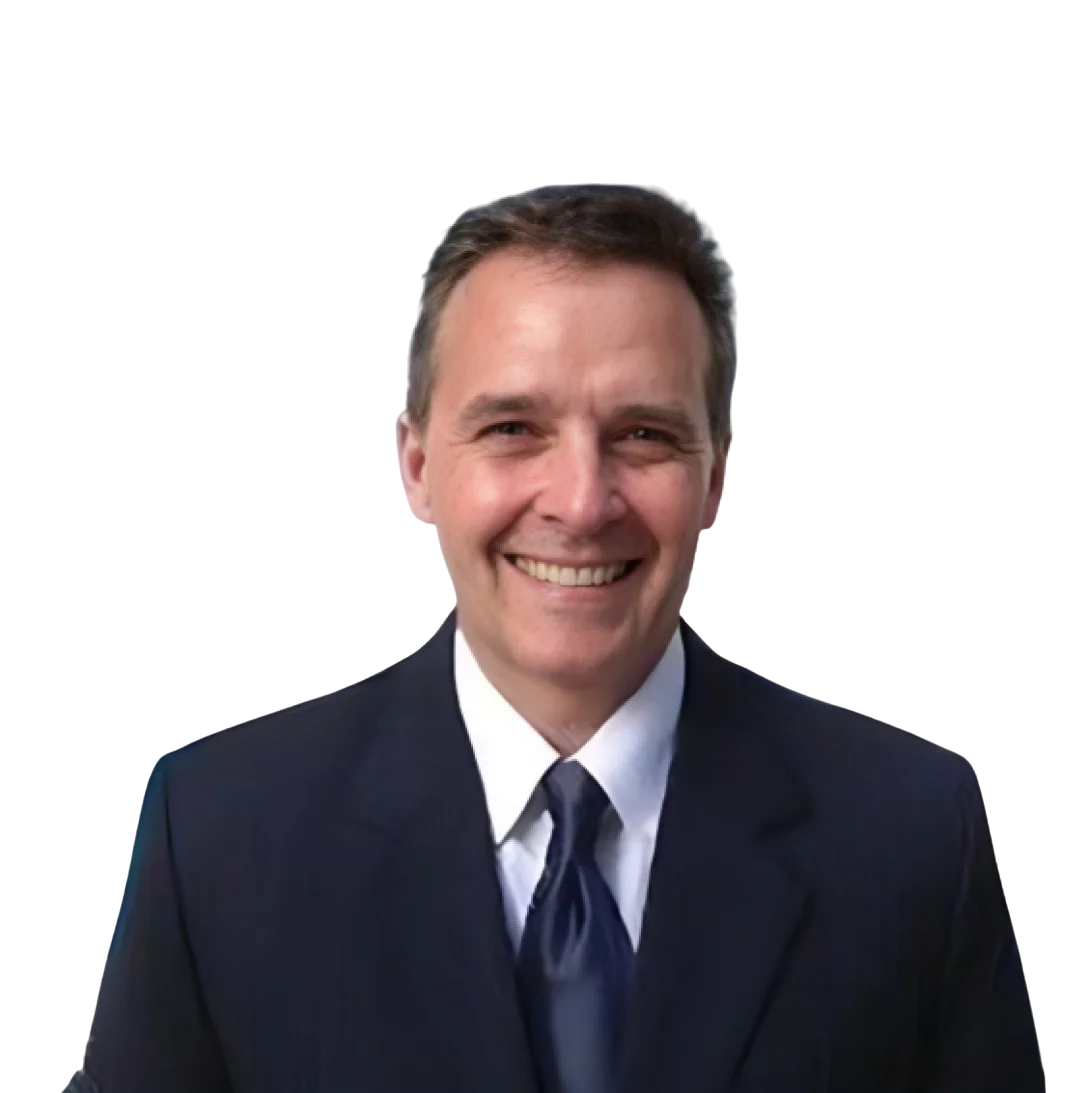
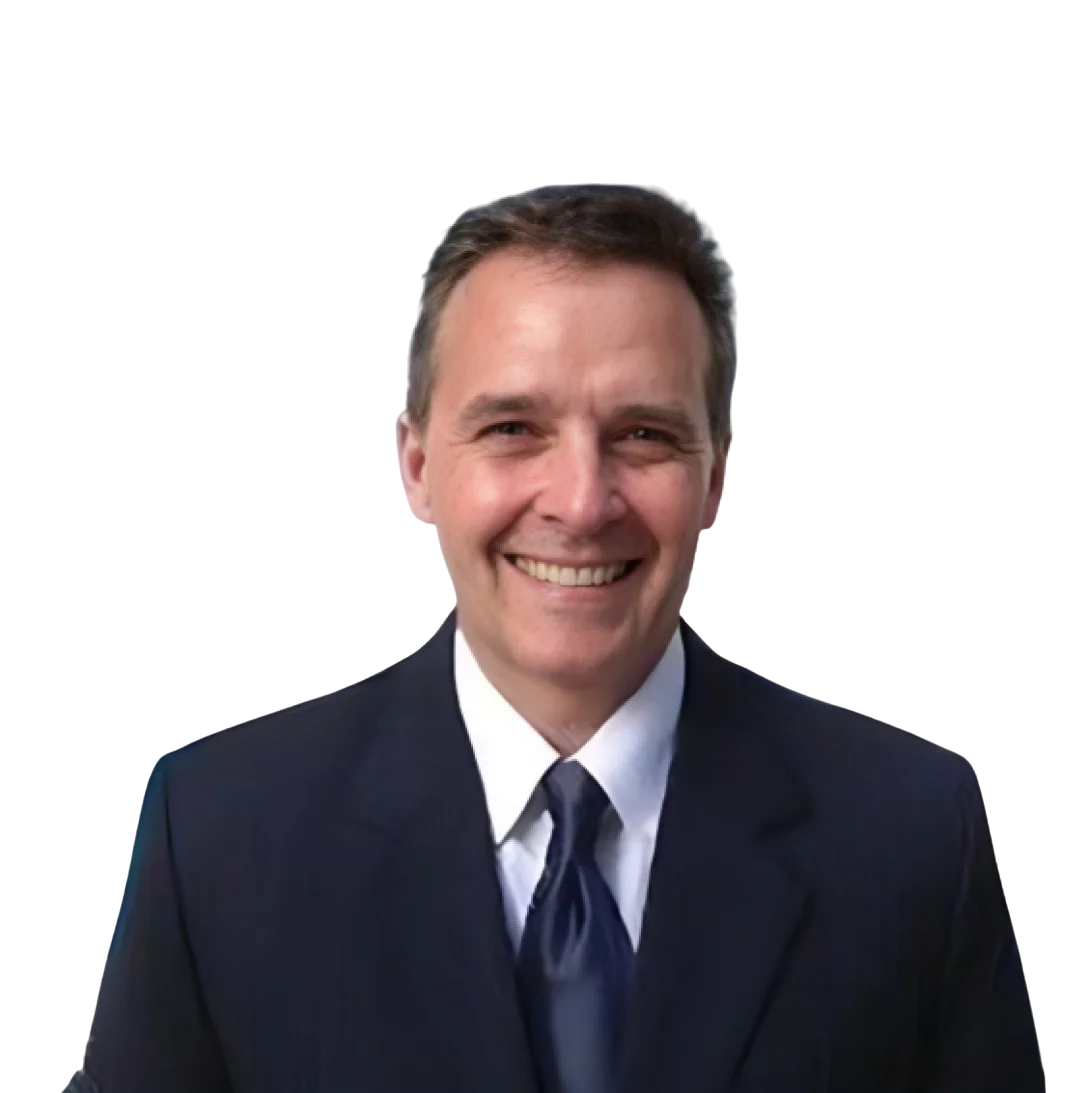
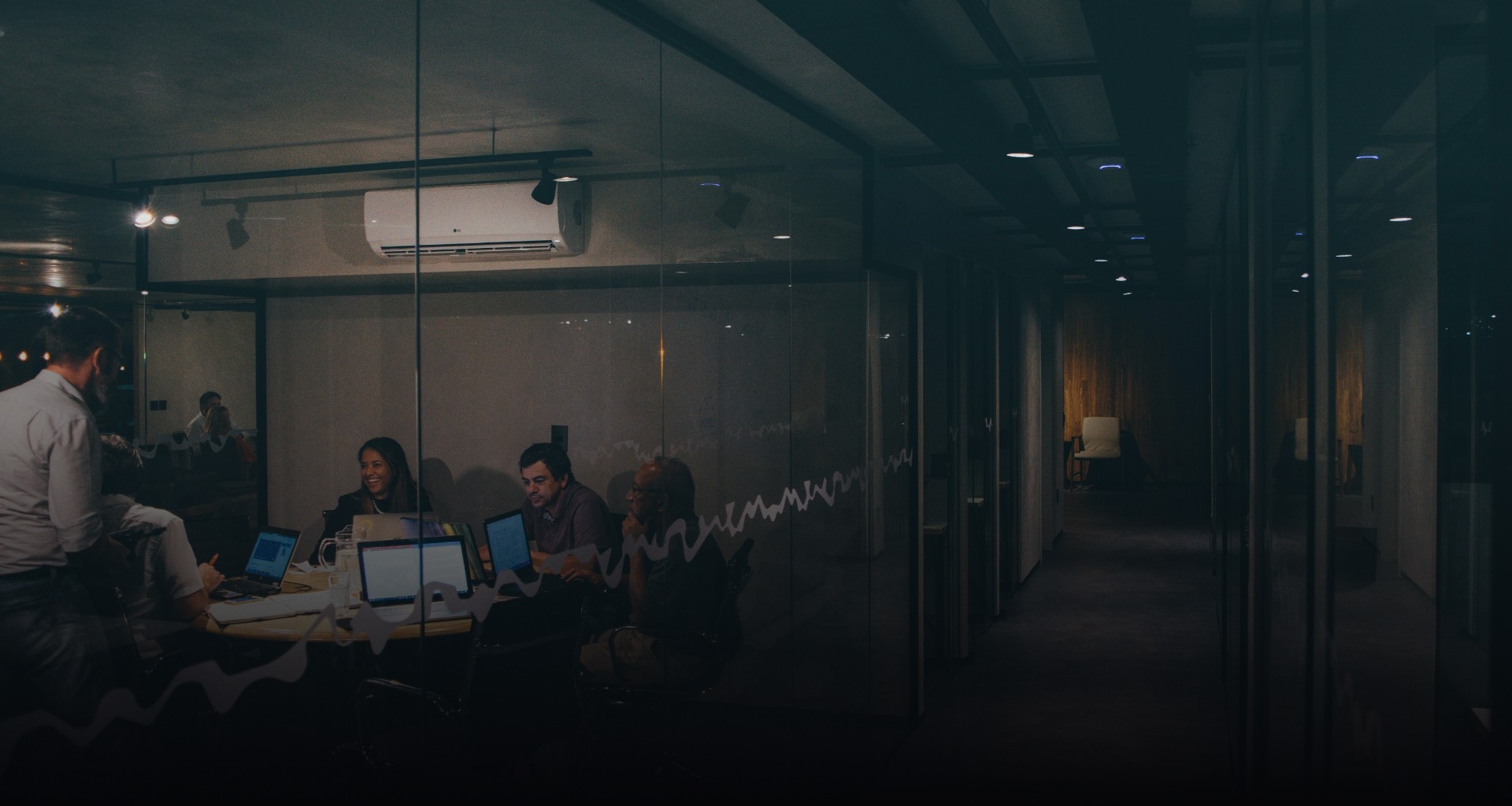
CASE STUDY: From Data Fragmentation to Delivery Excellence: A Case Study in Operational Improvement
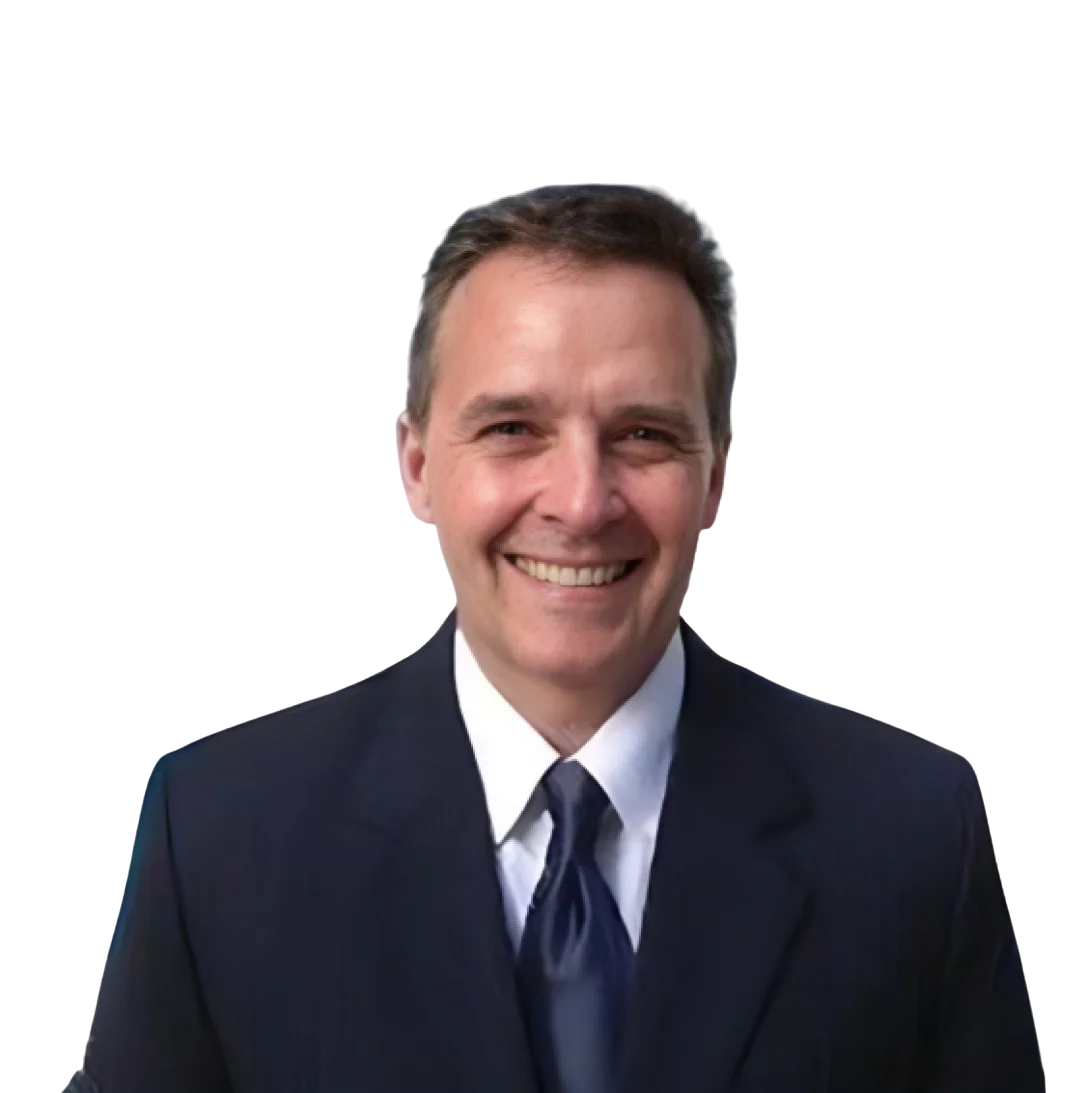
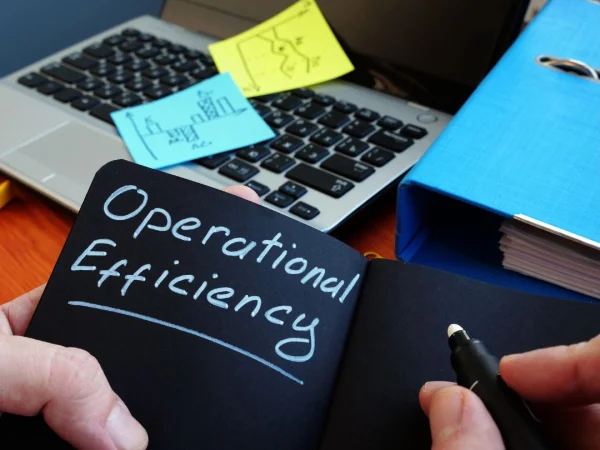
Challenge
When I first engaged with this company, they were grappling with data fragmentation. Their information was spread across multiple sources, making it difficult to:
1. Track late deliveries in detail
2. Utilize data effectively in day-to-day operations
3. Plan capacity and improve delivery performance
This situation was more than just an inconvenience - it was significantly hampering their operational efficiency.
My Approach
To address these issues, I developed a structured approach leveraging a combination of frameworks and methods:
Frameworks: I employed the Dolphin Method for alignment, LEAN principles, and Systems Thinking.
Methods: My toolkit included SIPOC, Value Stream Mapping (VSM), user stories, and advanced tech solutions like AWS S3 and Metabase analytics.
The Solution I Implemented
My solution consisted of three key components:
1. Data Integration: I combined data from their Manufacturing Execution System (MES) and JotForms into a single SQL database on AWS S3.
2. Analytics and Reporting: I implemented Metabase, a powerful analytics and reporting tool, to generate role-specific insights.
3. Predictive Modeling: I developed a statistical model to optimize production scheduling, taking into account multiple variables.
Key Discoveries
Throughout this process, we made several important realizations:
1. Short-term trends matter: I found that tracking on-time delivery performance over 7-day periods provided more actionable insights than monthly or quarterly averages.
2. Personalization is key: The role-based reporting I implemented significantly improved information relevance and accessibility.
3. Complexity requires sophisticated solutions: I realized that accurate lead-time planning necessitated a robust statistical model to account for multiple variables.
Measurable Improvements
The results of my initiative were significant:
1. Late deliveries decreased from double-digit to single-digit percentages.
2. I automated the data integration process, streamlining the consolidation.
3. We laid the groundwork for advanced analytics and machine learning.
4. The new lead time model I developed enhanced the accuracy of production scheduling.
Looking Ahead
Building on this success, I've recommended that the company implement machine learning techniques for even more advanced forecasting and capacity planning optimization.
The Takeaway
This case study illustrates how my strategic approach to data management and analytics can transform operations. By consolidating data, implementing robust analytics, and developing predictive models, we not only solved the immediate challenges but also positioned the company for continued improvement and innovation in its manufacturing operations.
From scattered data to streamlined operations, this journey serves as a blueprint for other companies facing similar challenges in today's data-driven business landscape.
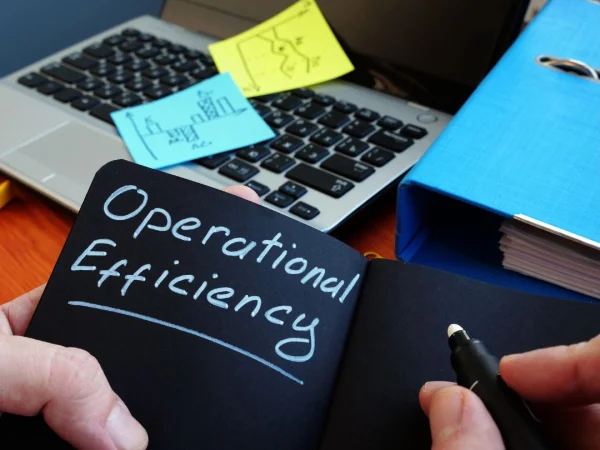
Challenge
When I first engaged with this company, they were grappling with data fragmentation. Their information was spread across multiple sources, making it difficult to:
1. Track late deliveries in detail
2. Utilize data effectively in day-to-day operations
3. Plan capacity and improve delivery performance
This situation was more than just an inconvenience - it was significantly hampering their operational efficiency.
My Approach
To address these issues, I developed a structured approach leveraging a combination of frameworks and methods:
Frameworks: I employed the Dolphin Method for alignment, LEAN principles, and Systems Thinking.
Methods: My toolkit included SIPOC, Value Stream Mapping (VSM), user stories, and advanced tech solutions like AWS S3 and Metabase analytics.
The Solution I Implemented
My solution consisted of three key components:
1. Data Integration: I combined data from their Manufacturing Execution System (MES) and JotForms into a single SQL database on AWS S3.
2. Analytics and Reporting: I implemented Metabase, a powerful analytics and reporting tool, to generate role-specific insights.
3. Predictive Modeling: I developed a statistical model to optimize production scheduling, taking into account multiple variables.
Key Discoveries
Throughout this process, we made several important realizations:
1. Short-term trends matter: I found that tracking on-time delivery performance over 7-day periods provided more actionable insights than monthly or quarterly averages.
2. Personalization is key: The role-based reporting I implemented significantly improved information relevance and accessibility.
3. Complexity requires sophisticated solutions: I realized that accurate lead-time planning necessitated a robust statistical model to account for multiple variables.
Measurable Improvements
The results of my initiative were significant:
1. Late deliveries decreased from double-digit to single-digit percentages.
2. I automated the data integration process, streamlining the consolidation.
3. We laid the groundwork for advanced analytics and machine learning.
4. The new lead time model I developed enhanced the accuracy of production scheduling.
Looking Ahead
Building on this success, I've recommended that the company implement machine learning techniques for even more advanced forecasting and capacity planning optimization.
The Takeaway
This case study illustrates how my strategic approach to data management and analytics can transform operations. By consolidating data, implementing robust analytics, and developing predictive models, we not only solved the immediate challenges but also positioned the company for continued improvement and innovation in its manufacturing operations.
From scattered data to streamlined operations, this journey serves as a blueprint for other companies facing similar challenges in today's data-driven business landscape.
Get in Touch to Transform Your Business Today
Schedule a FREE call with Rich Piech.
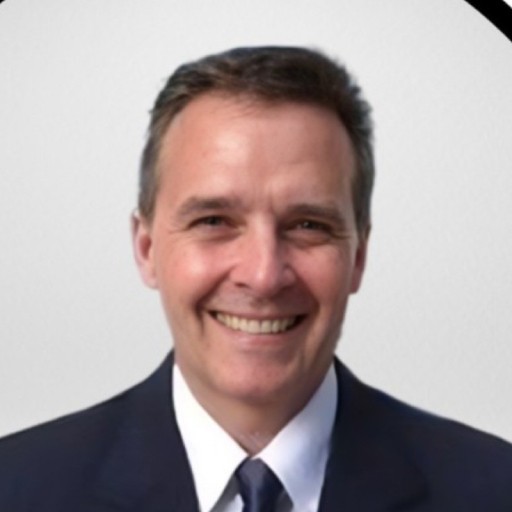
Get in Touch to Transform Your Business Today
Schedule a FREE call with Rich Piech.
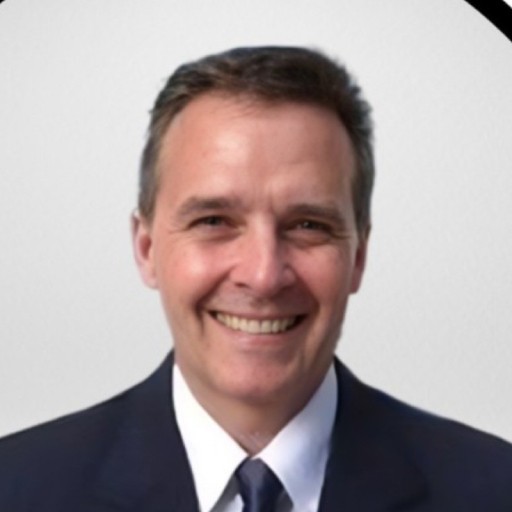
Get in Touch to Transform Your Business Today
Schedule a FREE call with Rich Piech.
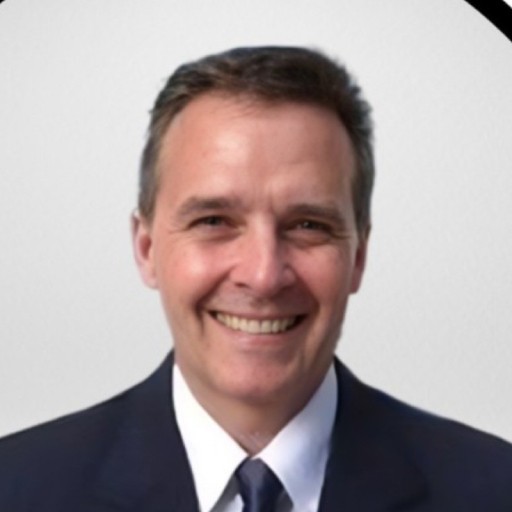
Challenge
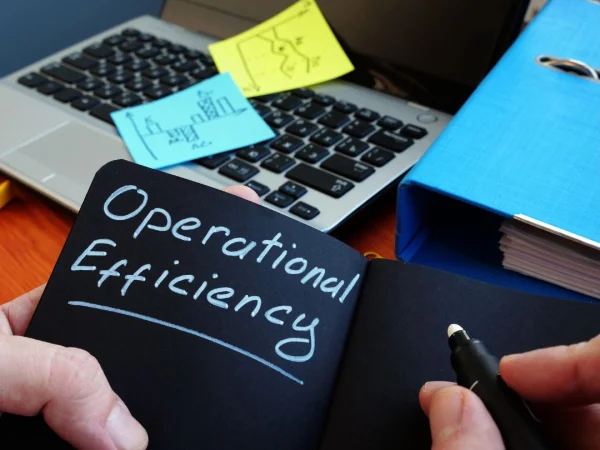
When I first engaged with this company, they were grappling with data fragmentation. Their information was spread across multiple sources, making it difficult to:
1. Track late deliveries in detail
2. Utilize data effectively in day-to-day operations
3. Plan capacity and improve delivery performance
This situation was more than just an inconvenience - it was significantly hampering their operational efficiency.
My Approach
To address these issues, I developed a structured approach leveraging a combination of frameworks and methods:
Frameworks: I employed the Dolphin Method for alignment, LEAN principles, and Systems Thinking.
Methods: My toolkit included SIPOC, Value Stream Mapping (VSM), user stories, and advanced tech solutions like AWS S3 and Metabase analytics.
The Solution I Implemented
My solution consisted of three key components:
1. Data Integration: I combined data from their Manufacturing Execution System (MES) and JotForms into a single SQL database on AWS S3.
2. Analytics and Reporting: I implemented Metabase, a powerful analytics and reporting tool, to generate role-specific insights.
3. Predictive Modeling: I developed a statistical model to optimize production scheduling, taking into account multiple variables.
Key Discoveries
Throughout this process, we made several important realizations:
1. Short-term trends matter: I found that tracking on-time delivery performance over 7-day periods provided more actionable insights than monthly or quarterly averages.
2. Personalization is key: The role-based reporting I implemented significantly improved information relevance and accessibility.
3. Complexity requires sophisticated solutions: I realized that accurate lead-time planning necessitated a robust statistical model to account for multiple variables.
Measurable Improvements
The results of my initiative were significant:
1. Late deliveries decreased from double-digit to single-digit percentages.
2. I automated the data integration process, streamlining the consolidation.
3. We laid the groundwork for advanced analytics and machine learning.
4. The new lead time model I developed enhanced the accuracy of production scheduling.
Looking Ahead
Building on this success, I've recommended that the company implement machine learning techniques for even more advanced forecasting and capacity planning optimization.
The Takeaway
This case study illustrates how my strategic approach to data management and analytics can transform operations. By consolidating data, implementing robust analytics, and developing predictive models, we not only solved the immediate challenges but also positioned the company for continued improvement and innovation in its manufacturing operations.
From scattered data to streamlined operations, this journey serves as a blueprint for other companies facing similar challenges in today's data-driven business landscape.
Get in Touch to Transform Your Business Today
Schedule a FREE call
with Rich Piech.
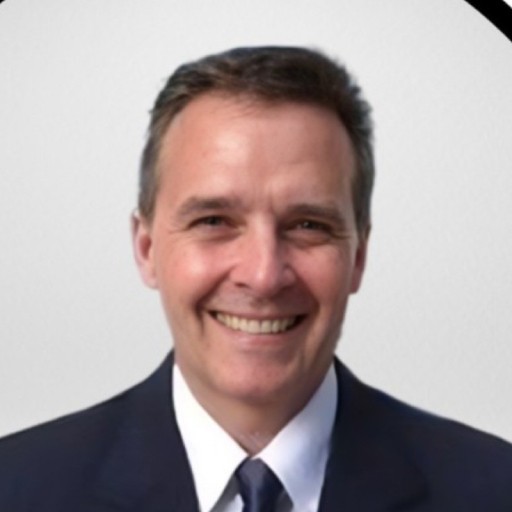
Get in Touch to Transform Your Business Today
Schedule a FREE call
with Rich Piech.
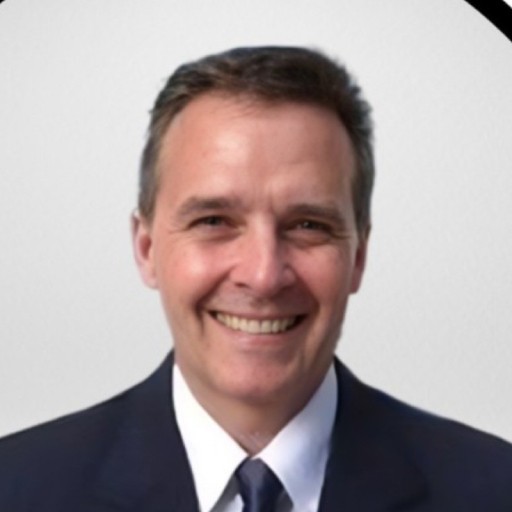