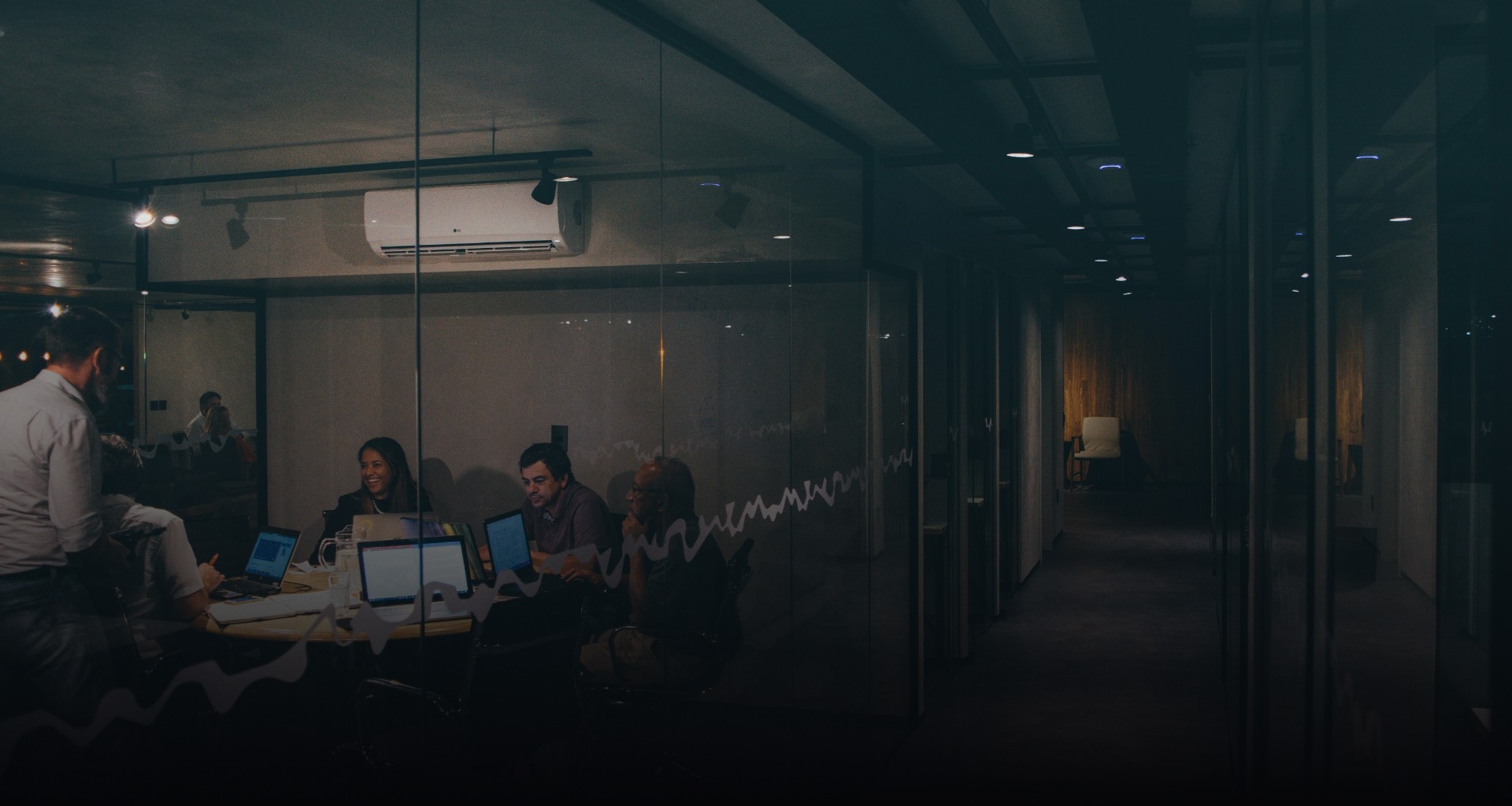
CASE STUDY: Lean Process Redesign Increases Inventory Check-In Throughput by 340% at Apparel Decoration Provider
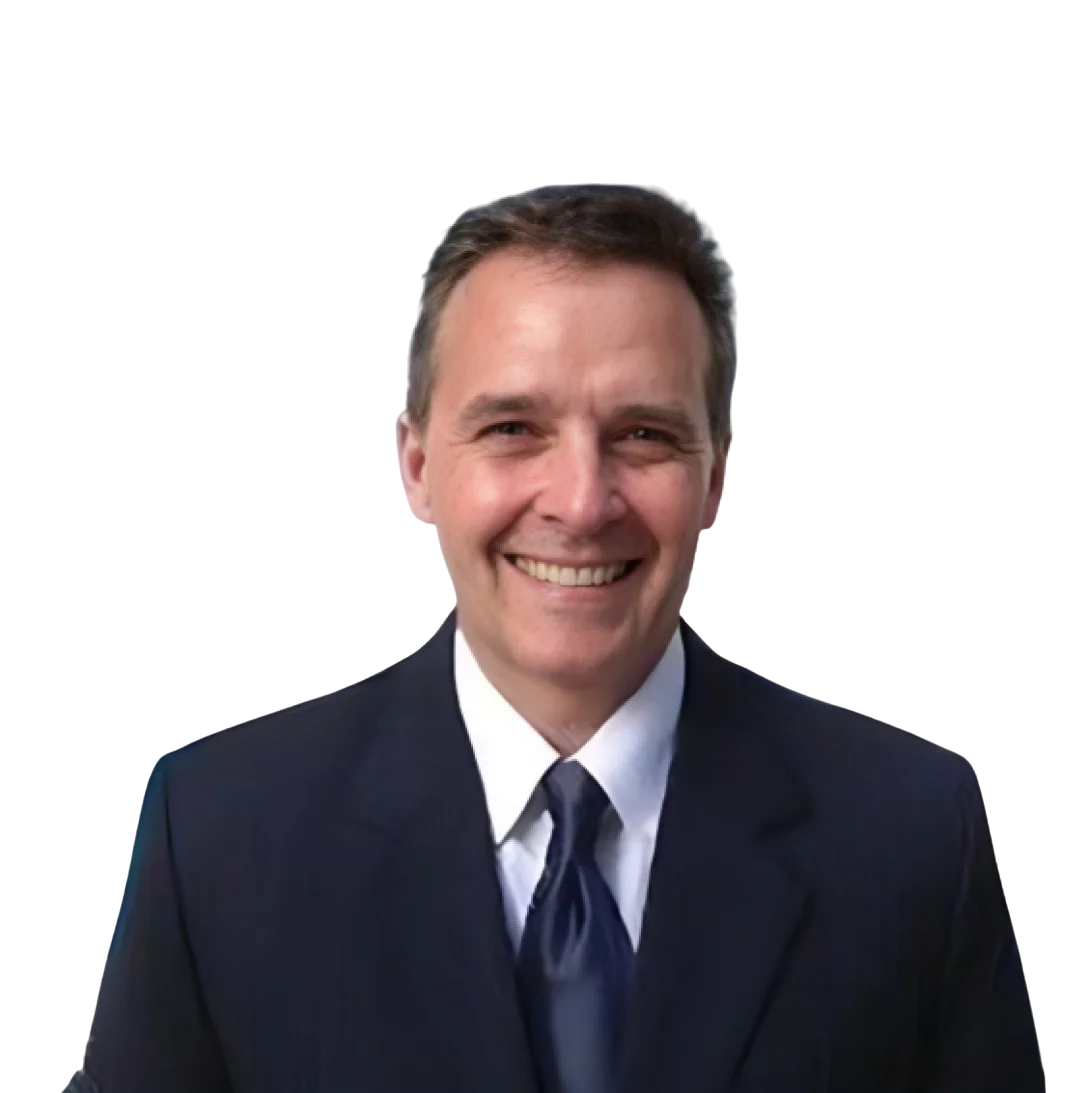
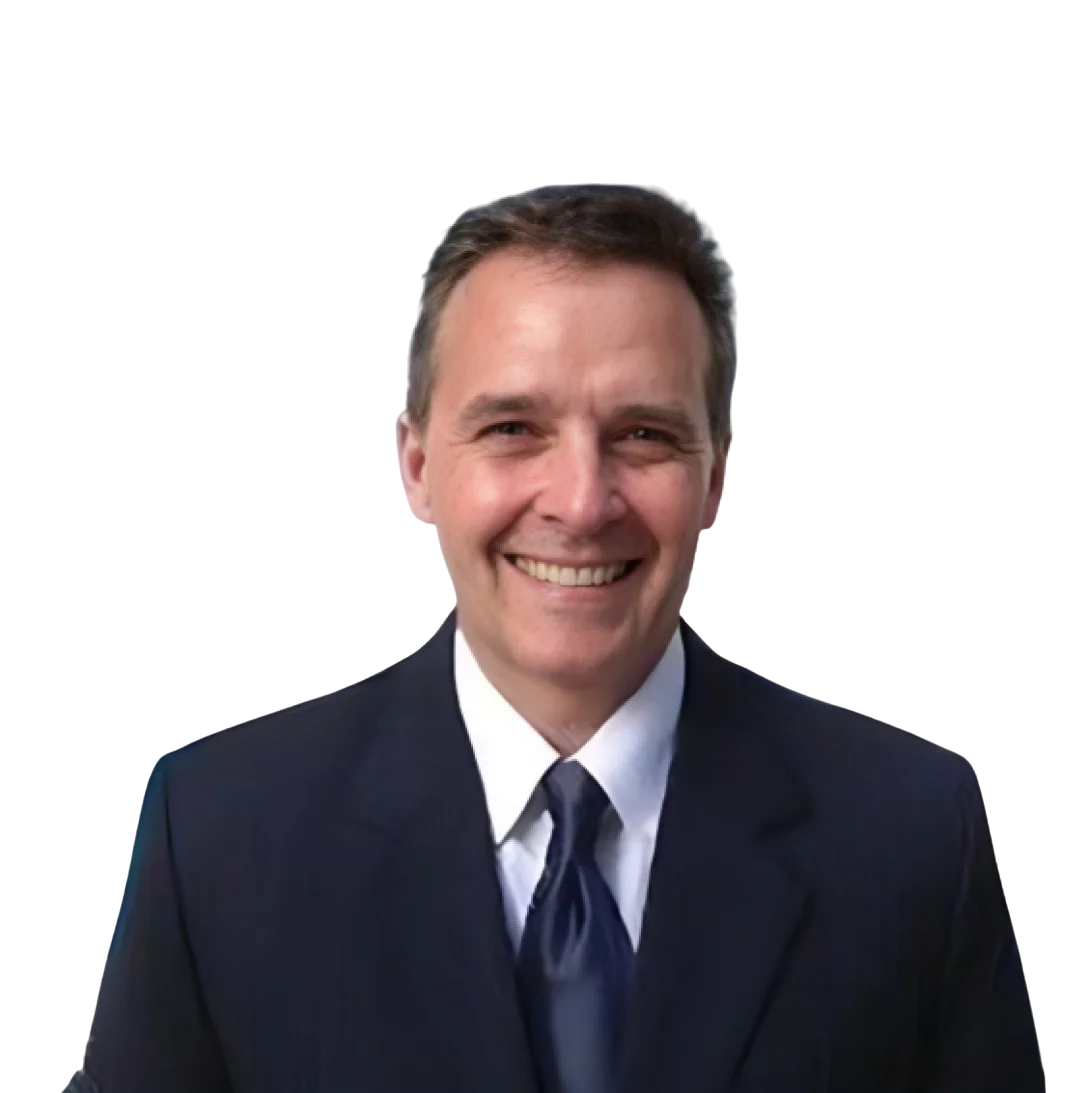
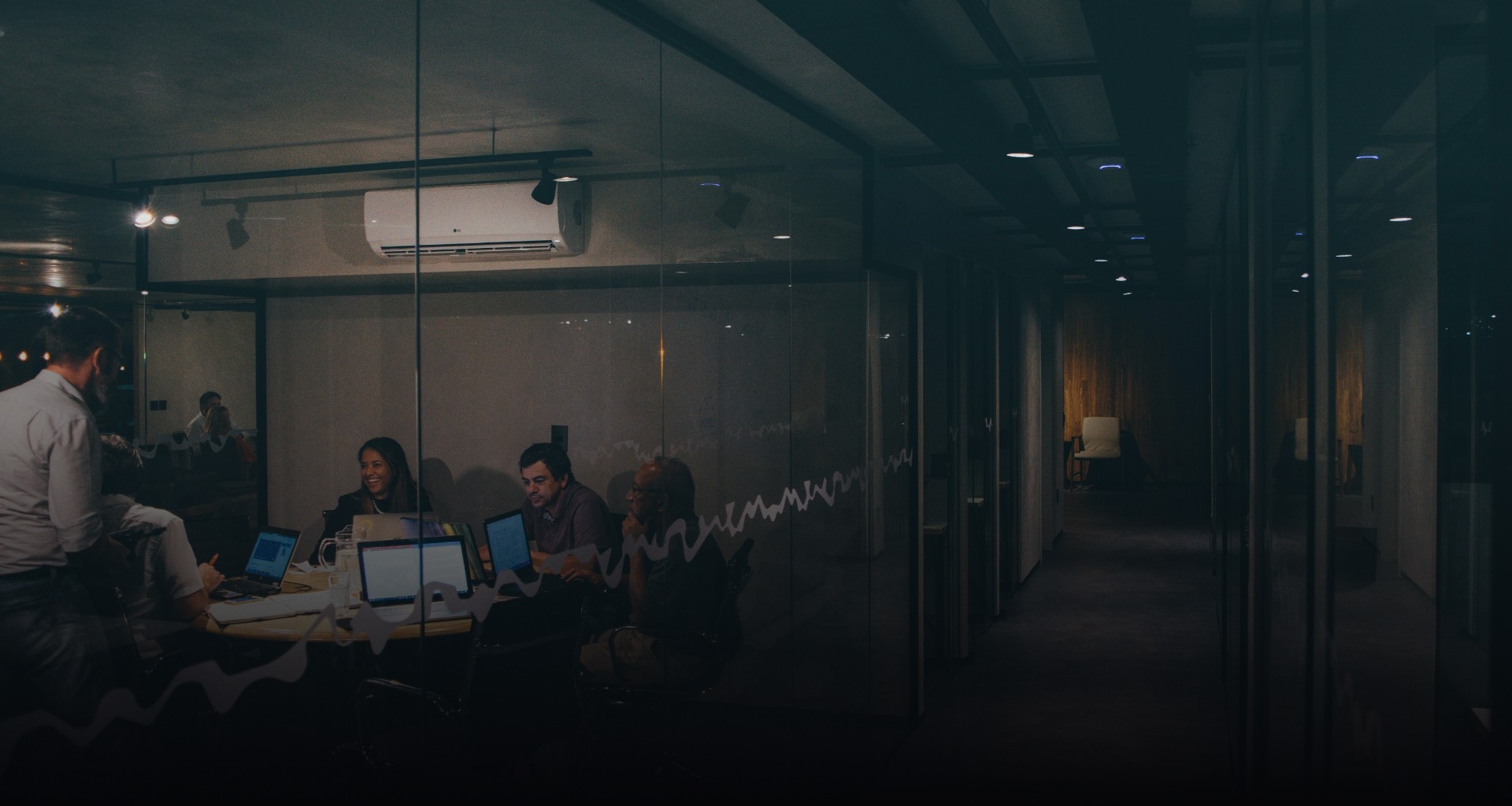
CASE STUDY: Lean Process Redesign Increases Inventory Check-In Throughput by 340% at Apparel Decoration Provider
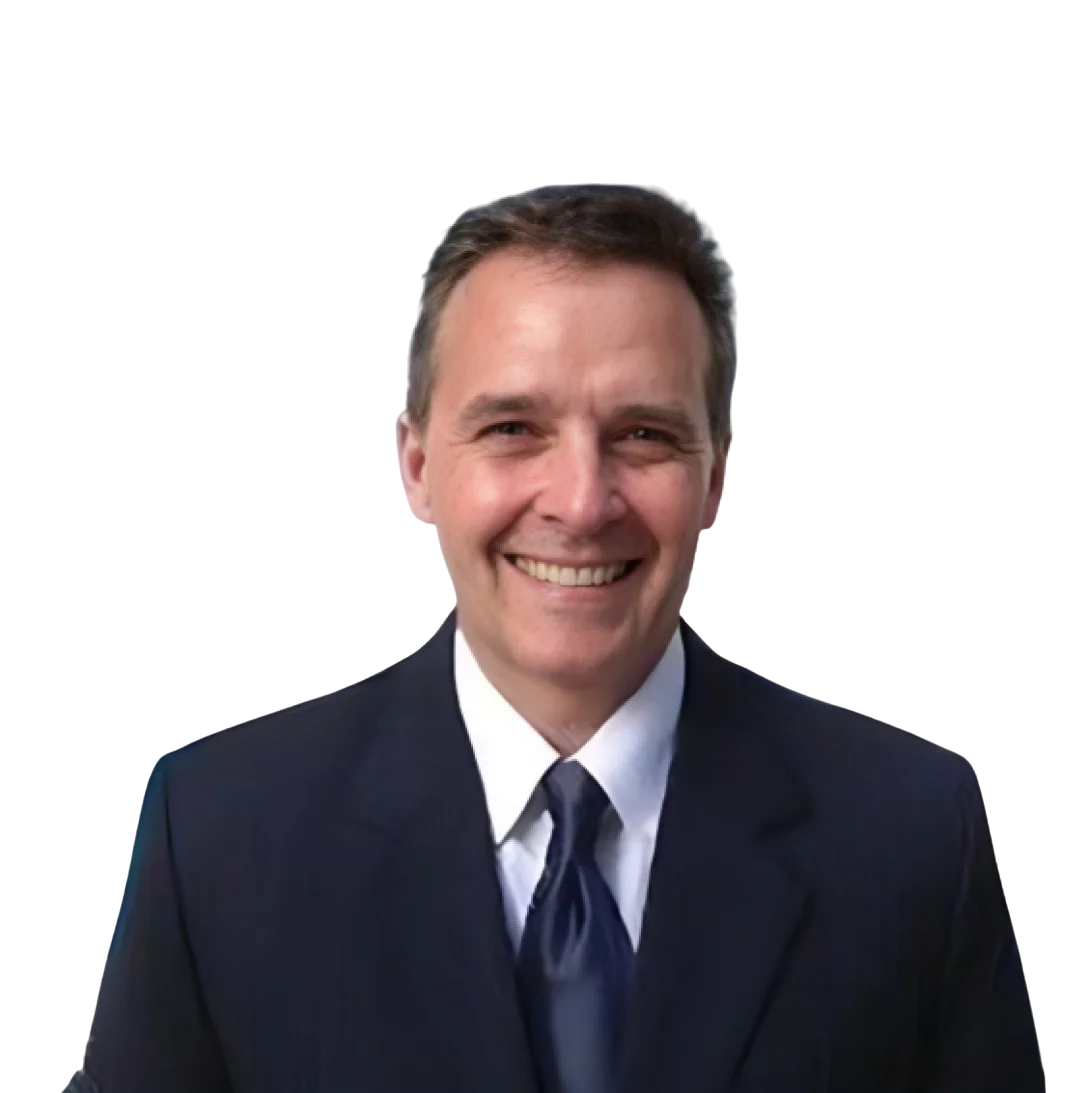
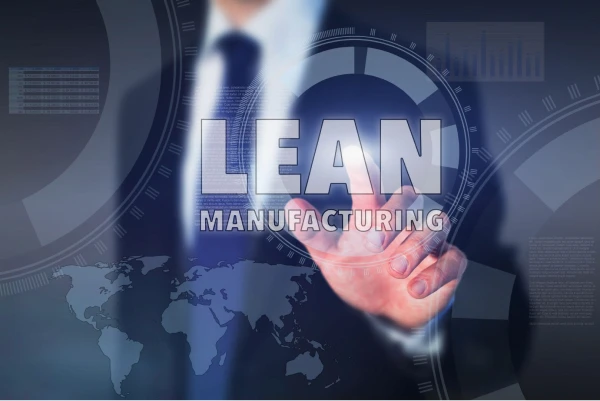
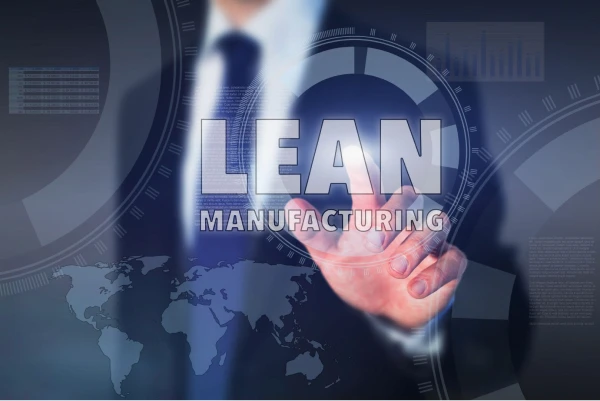
Industry Overview
Apparel decoration services is a labor-intensive industry, even small efficiency improvements can significantly impact productivity and profitability.
The Business Challenge
Previously, the inventory check-in cycle times caused bottlenecks that delayed getting work released to production floors...
Analyzing the Current State
The company took a structured approach to analyzing the current inventory check-in process using lean methodologies...
Baseline metrics were captured, including average items checked-in per person per day, adjusted for overtime pay.
Implementing Lean Solutions
Several process redesigns and physical changes were implemented based on the analysis...
The revised process applied lean principles like continuous flow, reduced motion waste, visual management, and pull production.
Achieved Results
The leaned inventory check-in process delivered outstanding productivity gains compared to the previous state for 500 boxes of inventory checked in.
- 25,570 feet (4.88 miles) of walking distance removed
- 44.74 direct labor hours saved
- 2,000 lift/placement motions eliminated
- 16 dolly trips across the facility removed
Ah-Ha Moment: Looking at Revised KPI
The "ah-ha" moment came when the team realized the old KPI of "items checked-in per person per day" was misleading. By accounting for overtime hours, they saw the true opportunity - the revised KPI "items checked-in per person per overtime hour" increased by 340.10%.
Results at Scale
With the new streamlined process, here is what can be saved:
- 511,400 feet (98 miles) less walking for 10,000 boxes
- Save 895 hours for 10,000 boxes
- Eliminate 40,000 lift/placements for 10,000 boxes
- Remove 320 dolly trips for 10,000 boxes
Before the kaizen, KPI data showed:
- Avg total items checked in per day: 1,023
- Avg items checked in per person per day: 196
- Accounting for 1.5x overtime pay: 66 items per person per day
After improvements:
- Avg total items checked in per day: 3,338 (226.30% increase)
- Avg items checked in per person per day: 556 (184.16% increase)
- Accounting for overtime: 289 items per person-hour (340.10% increase)
Benefits and Future Potential
The quantifiable improvements will lead to significant labor cost savings...
Get in Touch to Transform Your Business Today
Schedule a FREE call
with Rich Piech.
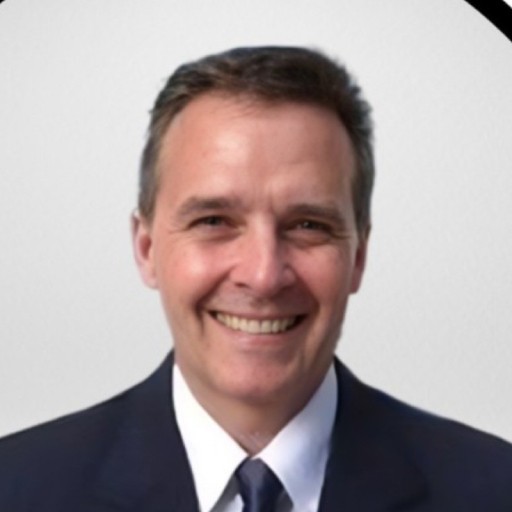
Get in Touch to Transform Your Business Today
Schedule a FREE call
with Rich Piech.
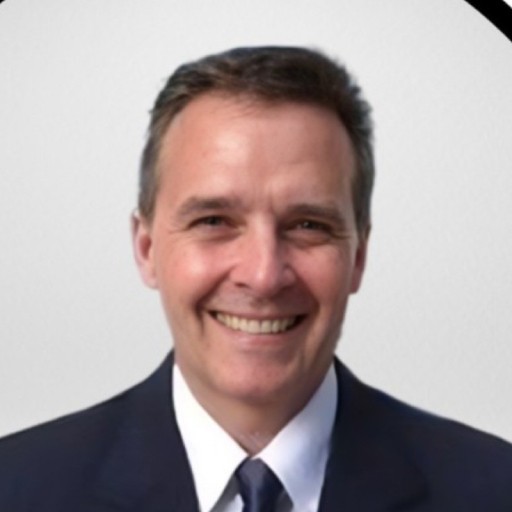
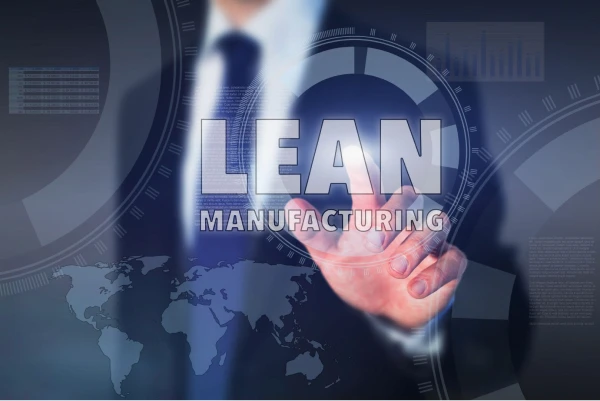
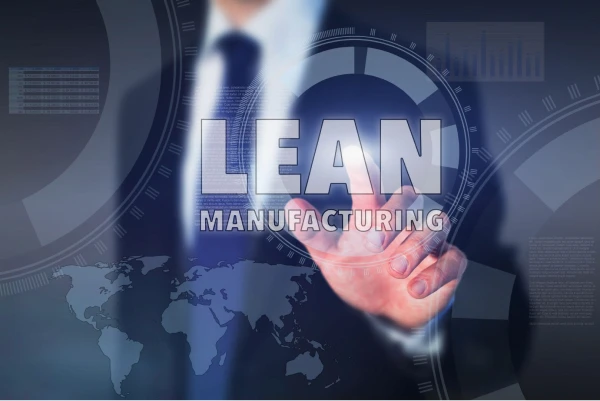
Industry Overview
Apparel decoration services is a labor-intensive industry, even small efficiency improvements can significantly impact productivity and profitability.
The Business Challenge
Previously, the inventory check-in cycle times caused bottlenecks that delayed getting work released to production floors...
Analyzing the Current State
The company took a structured approach to analyzing the current inventory check-in process using lean methodologies...
Baseline metrics were captured, including average items checked-in per person per day, adjusted for overtime pay.
Implementing Lean Solutions
Several process redesigns and physical changes were implemented based on the analysis...
The revised process applied lean principles like continuous flow, reduced motion waste, visual management, and pull production.
Achieved Results
The leaned inventory check-in process delivered outstanding productivity gains compared to the previous state for 500 boxes of inventory checked in.
- 25,570 feet (4.88 miles) of walking distance removed
- 44.74 direct labor hours saved
- 2,000 lift/placement motions eliminated
- 16 dolly trips across the facility removed
Ah-Ha Moment: Looking at Revised KPI
The "ah-ha" moment came when the team realized the old KPI of "items checked-in per person per day" was misleading. By accounting for overtime hours, they saw the true opportunity - the revised KPI "items checked-in per person per overtime hour" increased by 340.10%.
Results at Scale
With the new streamlined process, here is what can be saved:
- 511,400 feet (98 miles) less walking for 10,000 boxes
- Save 895 hours for 10,000 boxes
- Eliminate 40,000 lift/placements for 10,000 boxes
- Remove 320 dolly trips for 10,000 boxes
Before the kaizen, KPI data showed:
- Avg total items checked in per day: 1,023
- Avg items checked in per person per day: 196
- Accounting for 1.5x overtime pay: 66 items per person per day
After improvements:
- Avg total items checked in per day: 3,338 (226.30% increase)
- Avg items checked in per person per day: 556 (184.16% increase)
- Accounting for overtime: 289 items per person-hour (340.10% increase)
Benefits and Future Potential
The quantifiable improvements will lead to significant labor cost savings...
Get in Touch to Transform Your Business Today
Schedule a FREE call with Rich Piech.
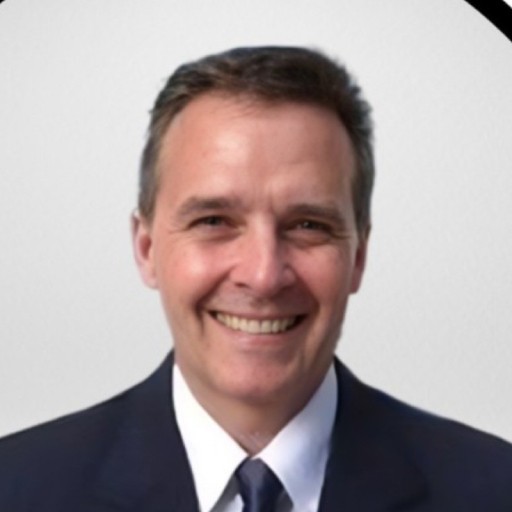
Get in Touch to Transform Your Business Today
Schedule a FREE call with Rich Piech.
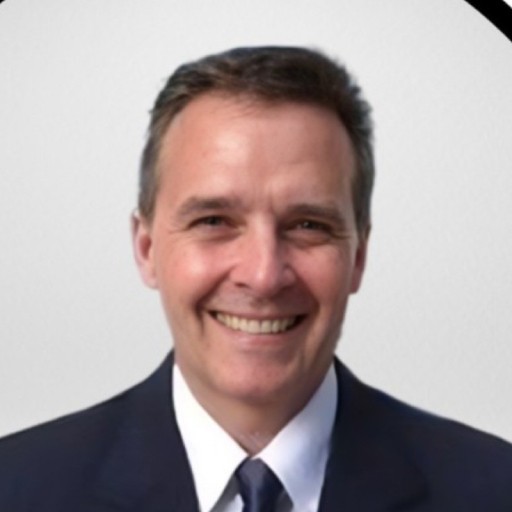
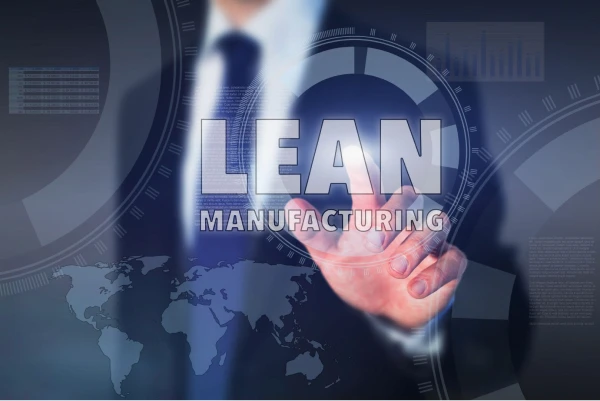
Industry Overview
Apparel decoration services is a labor-intensive industry, even small efficiency improvements can significantly impact productivity and profitability.
The Business Challenge
Previously, the inventory check-in cycle times caused bottlenecks that delayed getting work released to production floors...
Analyzing the Current State
The company took a structured approach to analyzing the current inventory check-in process using lean methodologies...
Baseline metrics were captured, including average items checked-in per person per day, adjusted for overtime pay.
Implementing Lean Solutions
Several process redesigns and physical changes were implemented based on the analysis...
The revised process applied lean principles like continuous flow, reduced motion waste, visual management, and pull production.
Achieved Results
The leaned inventory check-in process delivered outstanding productivity gains compared to the previous state for 500 boxes of inventory checked in.
- 25,570 feet (4.88 miles) of walking distance removed
- 44.74 direct labor hours saved
- 2,000 lift/placement motions eliminated
- 16 dolly trips across the facility removed
Ah-Ha Moment: Looking at Revised KPI
The "ah-ha" moment came when the team realized the old KPI of "items checked-in per person per day" was misleading. By accounting for overtime hours, they saw the true opportunity - the revised KPI "items checked-in per person per overtime hour" increased by 340.10%.
Results at Scale
With the new streamlined process, here is what can be saved:
- 511,400 feet (98 miles) less walking for 10,000 boxes
- Save 895 hours for 10,000 boxes
- Eliminate 40,000 lift/placements for 10,000 boxes
- Remove 320 dolly trips for 10,000 boxes
Before the kaizen, KPI data showed:
- Avg total items checked in per day: 1,023
- Avg items checked in per person per day: 196
- Accounting for 1.5x overtime pay: 66 items per person per day
After improvements:
- Avg total items checked in per day: 3,338 (226.30% increase)
- Avg items checked in per person per day: 556 (184.16% increase)
- Accounting for overtime: 289 items per person-hour (340.10% increase)
Benefits and Future Potential
The quantifiable improvements will lead to significant labor cost savings...
Get in Touch to Transform Your Business Today
Schedule a FREE call with Rich Piech.
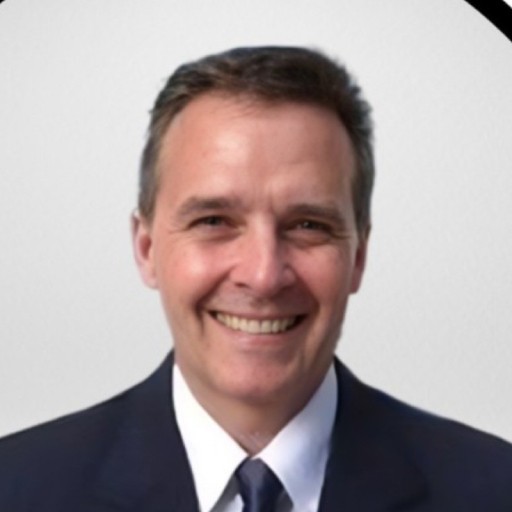